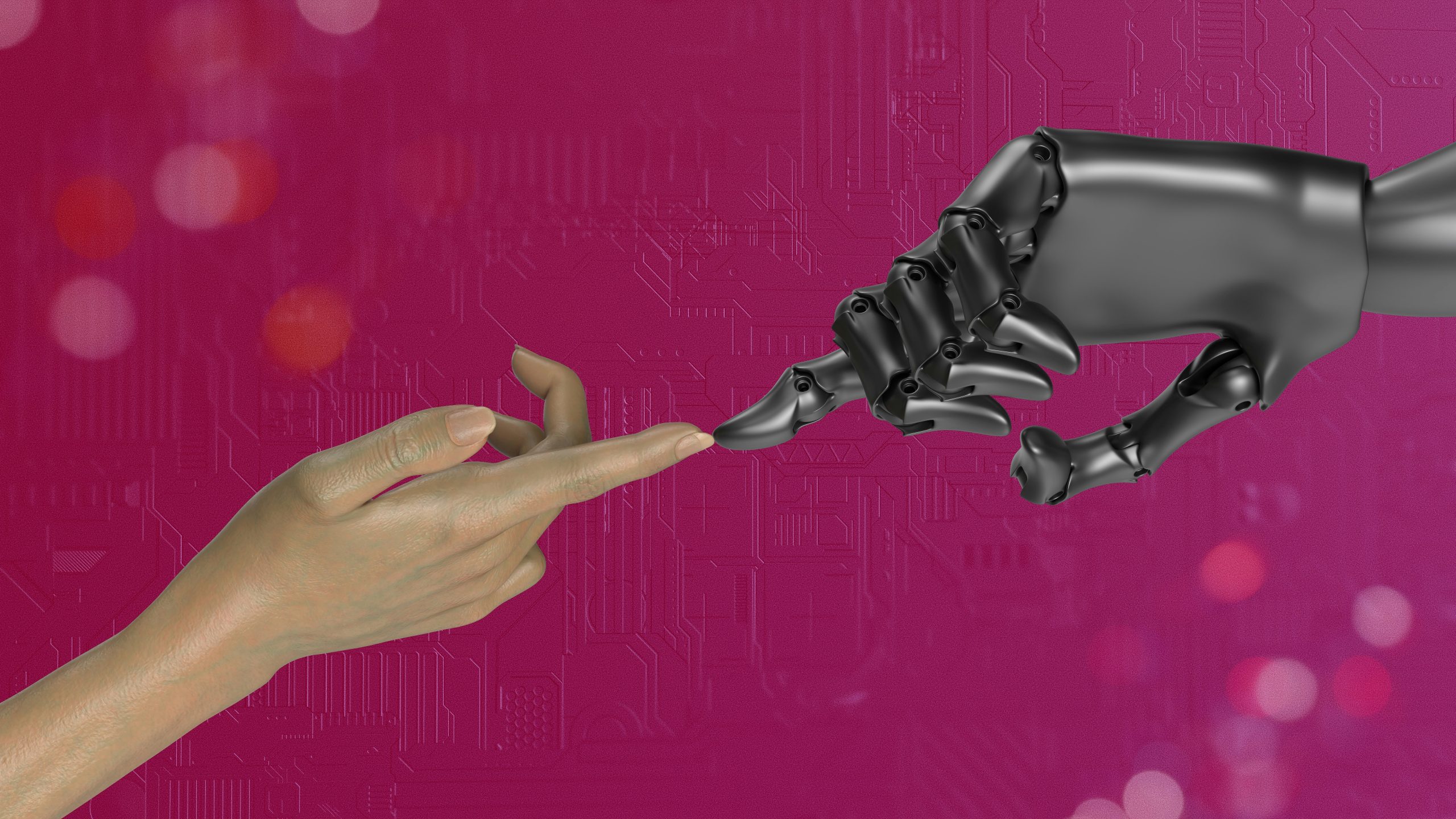
Introduction to Automatic Carton Formers
In today’s fast-paced manufacturing world, efficiency is the name of the game. With increasing demands for quick turnaround times and high-quality packaging, businesses are constantly on the lookout for solutions that streamline their processes. Enter the automatic carton former—an unsung hero in large-scale production lines. This innovative machine takes care of one of the most tedious tasks in packaging: forming cartons. By automating this step, companies can save time, reduce labor costs, and improve overall productivity.
Imagine a bustling production line where every second counts. The last thing you want is to waste precious minutes on manual carton assembly when there are more critical tasks at hand. Automatic carton formers provide a seamless solution by quickly transforming flat sheets into perfectly formed boxes ready for filling and sealing. As we delve deeper into this topic, we’ll explore how these machines work and why they’ve become essential assets in modern manufacturing settings. Whether you’re a seasoned industry pro or just starting out, understanding these powerful tools could change your approach to production forever.
Benefits of Using an Automatic Carton Former in Production Lines
Using an automatic carton former in production lines streamlines packaging processes significantly. It reduces the time spent on manual folding and assembling cartons, allowing staff to focus on more critical tasks.
This technology enhances carton former consistency in carton formation. Each box is created uniformly, leading to fewer errors during packing and shipping. Such precision minimizes product damage and improves overall quality control.
Cost savings are another major benefit. By automating this process, companies can reduce labor costs while increasing output rates. The return on investment often becomes apparent quickly as productivity rises.
Automatic carton formers also contribute to a safer work environment. With less manual handling involved, there’s a lower risk of workplace injuries related to repetitive strain or accidents associated with traditional packing methods.
Additionally, these machines adapt easily to various carton sizes and styles, making them versatile for diverse production needs without extensive downtime for reconfiguration.
How Does an Automatic Carton Former Work?
An automatic carton former operates with precision and speed, streamlining the packaging process. It starts by feeding flat cardboard sheets into the machine.
Sensors detect the sheet’s position, ensuring accurate alignment. As the cardboard moves forward, mechanical arms fold it into a pre-defined shape.
Adhesives or locking mechanisms are then applied to secure the corners of each carton firmly. This eliminates any manual labor required for folding and sealing.
Once formed, these cartons are automatically loaded onto a conveyor system, ready for product filling. The entire process is synchronized to maintain high throughput rates without compromising quality.
With advanced technology like PLC controls and touchscreens, operators can easily adjust settings for different box sizes or styles on-the-fly. This adaptability makes it suitable for various production environments as demand fluctuates throughout operations.
Key Features to Look for When Choosing an Automatic Carton Former
When selecting an automatic carton former for large-scale production, several key features stand out. First, look for speed and efficiency. A machine that can form cartons quickly will significantly enhance your overall output.
Next, consider the versatility of the equipment. It should accommodate various carton sizes and styles to adapt to different products without requiring extensive adjustments.
Durability is crucial too. The construction materials and design must withstand continuous use in a demanding environment.
Ease of operation plays a vital role as well. User-friendly interfaces allow operators to manage settings effortlessly, reducing training time and minimizing errors.
Maintenance options are important. Choose a model with easy access to components for quick repairs or servicing without disrupting production flow. These features collectively ensure optimal performance in your manufacturing process.
Case Studies: Real-Life Examples of Improved Efficiency with Automatic Carton Formers
One notable case involves a beverage manufacturer struggling with high labor costs and inconsistent carton quality. After integrating an automatic carton former into their production line, they reported a 30% increase in efficiency. The machine consistently produced perfectly formed cartons, reducing waste significantly.
Another example comes from the electronics industry. A company facing bottlenecks during packaging switched to an automatic carton former. This transition led to faster turnaround times and improved product protection during shipping. They enjoyed smoother operations and reduced damage claims.
A third case highlights a cosmetic brand that needed flexibility for various package sizes. By adopting an adjustable automatic carton former, they streamlined their process without sacrificing speed or quality, allowing them to meet seasonal demand fluctuations seamlessly. These real-world applications showcase how effective these machines can be in enhancing operational excellence across diverse sectors.
Common Challenges and Solutions when Using an Automatic Carton Former
Using an automatic carton former can streamline operations, but challenges often arise. One common issue is misalignment of cartons during the forming process. This can technology lead to jams and production delays.
Regular maintenance is vital for preventing this problem. Ensuring that all components are well-lubricated and free from debris minimizes mechanical errors.
Another challenge involves inconsistent carton sizes or types. Operators might struggle with setup changes when switching products. Implementing a user-friendly interface or quick-change features can significantly reduce downtime.
Additionally, employee training plays a crucial role in overcoming these hurdles. Well-trained staff will better understand machine capabilities and troubleshooting techniques, enhancing overall efficiency.
Integration with existing systems may pose initial difficulties. Collaborating closely with manufacturers on installation ensures smooth compatibility within your production line’s ecosystem.
Conclusion: Why an Automatic Carton Former is a Valuable Investment for Production Lines
Investing in an automatic carton former for large-scale production can transform your packaging process. With enhanced efficiency, reduced labor costs, and consistent quality, these machines are a game-changer for manufacturers.
An automatic carton former streamlines the packing operation by quickly forming cartons ready for filling. This not only saves time but also minimizes human error. As production demands increase, having reliable equipment becomes essential to meet market needs without sacrificing quality.
Moreover, advanced features such as adjustable settings and compatibility with various carton sizes ensure versatility in operations. When coupled with case studies showcasing real-life improvements in productivity and cost savings, it’s clear that adopting this technology offers measurable benefits.
Embracing automation is more than just keeping up with industry trends; it’s about future-proofing your business. The right equipment can lead to sustained growth while enhancing the overall workflow of production lines. Investing in an automatic carton former is not merely a choice; it’s a strategic decision that positions businesses for success in today’s competitive landscape.