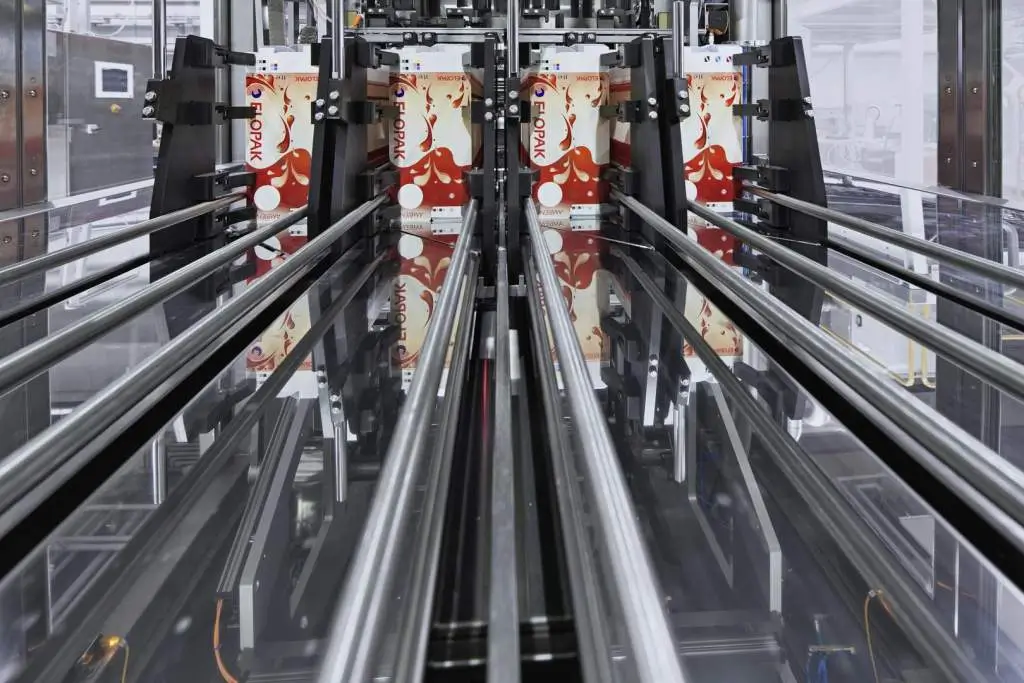
Introduction to filling machines and their uses in industrial settings
Filling machines play a crucial role in the heart of industrial production. From food packaging to pharmaceuticals, these machines ensure that products are dispensed accurately and efficiently. With an increasing demand for high-quality output, choosing the right filling machine can make all the difference in your operation’s success.
When it comes to selecting a durable filling machine for industrial use, there’s more at stake than just price. You need a reliable partner that can handle rigorous workloads while maintaining precision and consistency. As industries evolve, so do the technologies behind these machines. Let’s explore what you should look for when investing in this essential equipment and how it can elevate your production line to new heights.
Key Factors in Choosing the Right Filling Machine
When selecting a durable filling machine for industrial use, it’s crucial to evaluate the materials used in its construction. Robust components ensure longevity and withstand rigorous operations.
Next, consider whether you need a manual or automatic operation. Automatic machines typically filling machine enhance efficiency but may require more initial investment and maintenance.
The production capacity and speed also play pivotal roles. Assess your production demands to find a machine that can keep pace without compromising quality.
Compatibility is key. Ensure the filling machine handles various product types—liquids, powders, or granules—to maximize versatility in your manufacturing processes. Each factor contributes significantly to achieving optimal performance in an industrial setting.
A. Materials used in construction
The materials used in the construction of filling machines for industrial use play a pivotal role in their longevity and performance. Stainless steel is a prime choice due to its corrosion resistance and easy cleaning properties. This makes it ideal for industries like food and pharmaceuticals, where hygiene is paramount.
Another material often found in high-quality machines is aluminum, known for being lightweight yet robust. It can withstand heavy usage without compromising structural integrity.
Plastic components may also be present but should be chosen carefully. High-density polyethylene (HDPE) or polypropylene are excellent options because they offer durability while remaining cost-effective.
Evaluating these materials helps ensure that your filling machine will endure the rigors of daily operations while maintaining efficiency. Choosing wisely means investing in equipment that stands the test of time, thus reducing long-term costs associated with repairs or replacements.
B. Type of operation (manual vs automatic)
When selecting a durable filling machine for industrial use, the type of operation is crucial. You have two primary options: manual and automatic systems.
Manual machines require operators to oversee each step. This can be beneficial in smaller operations where precision is key. However, it may become tedious as production demands increase. Human error could lead to inconsistencies if not monitored closely.
On the other hand, automatic filling machines streamline the process significantly. They allow for higher throughput with minimal intervention needed from staff. These systems often come equipped with advanced technology that ensures accuracy and efficiency.
Choosing between manual and automatic depends on your business needs. Consider factors like production volume and available workforce when making this decision. Each has its advantages, so understanding how they align with your goals is essential.
C. Production capacity and speed
When selecting a durable filling machine for industrial use, production capacity and speed are crucial factors. These elements determine how efficiently your operation can meet demand.
Assess the volume of products you need to fill daily. Machines come with varying capacities, so finding one that matches your production goals is essential. A system that operates too slowly can create bottlenecks, impacting overall productivity.
Speed also plays a significant role in workflow efficiency. Some machines offer rapid cycles without compromising accuracy, which is vital for maintaining quality standards.
Consider how often you anticipate needing to scale up your operations as well. Investing in a machine that allows for flexibility in both speed and capacity ensures you won’t outgrow it quickly or waste resources on unnecessary upgrades later on.
D. Compatibility with different types of products
When selecting a filling machine for industrial use, compatibility with various products is crucial. Different industries handle diverse materials, from liquids to powders and granules. Your chosen machine must effectively accommodate these variations.
Consider the viscosity of your product. A thick paste demands different handling compared to a thin liquid. Ensure the filling machine can manage such differences without compromising accuracy or speed.
Additionally, the nature of your product matters. For example, food-grade requirements necessitate machines that meet health standards and prevent contamination. technology Pharmaceutical products often require even stricter compliance protocols.
Think about future needs. If you plan to expand your product line, opt for a versatile filling machine designed for adaptability—one that can easily switch between different formulations or package sizes without extensive modifications.
Types of filling machines available for industrial use
Filling machines come in various types, each designed for specific applications. Piston fillers are popular for their precision. They work by drawing a set volume of product into a cylinder and then dispensing it through a nozzle. This makes them ideal for thick liquids and pastes.
Gravity fillers rely on the force of gravity to fill containers. These are best suited for thin or free-flowing liquids, like water or juice. The simplicity of their design allows for easy operation and maintenance.
Pump fillers utilize mechanical pumps to move products from one place to another. This type is versatile and can handle both viscous materials and larger volumes efficiently.
Choosing the right filling machine hinges on understanding your product needs. Each type serves distinct purposes, ensuring that industrial operations run smoothly while maintaining quality standards.
A. Piston fillers
Piston fillers are a popular choice in the industrial filling machine landscape. They utilize a piston mechanism to draw and dispense liquid products efficiently. This design ensures precise volume control, making them ideal for applications requiring accuracy.
These machines excel with thicker liquids or viscous substances, such as sauces, creams, and oils. Their robust construction allows them to handle challenging materials while maintaining consistent output.
One of the standout features of piston fillers is their versatility. They can be easily adjusted for different fill sizes, catering to varying production needs without extensive downtime.
Moreover, they often come equipped with easy-to-use controls that enhance operational efficiency. As industries evolve and demands increase, piston fillers remain a dependable option in many manufacturing settings.
B. Gravity fillers
Gravity fillers operate on a simple yet effective principle. They rely on the force of gravity to dispense liquids into containers. This design makes them an excellent choice for products that are non-viscous and flow easily, such as water, juice, or light oils.
These machines typically feature a reservoir positioned above the filling nozzle. As product levels decrease, gravity pulls more liquid down through the nozzle into the waiting container below. The simplicity of this mechanism means fewer moving parts and less maintenance over time.
One key advantage is their versatility in various container shapes and sizes. Gravity fillers can handle everything from small bottles to larger jugs with minimal adjustments required.
Moreover, they’re often cost-effective compared to more complex filling systems. Their straightforward operation allows manufacturers to keep production running smoothly without frequent downtime or extensive training for staff members.
C. Pump fillers
Pump fillers are a versatile option in the realm of durable filling machines for industrial use. They work by transferring product through a pump, providing precise control over volume and flow rates. This makes them ideal for handling viscous liquids such as oils, creams, or sauces.
One of their standout features is adaptability. Pump fillers can accommodate various container shapes and sizes with minimal adjustments. This flexibility allows businesses to scale production without significant downtime.
Moreover, they often include settings that ensure consistent fill levels across batches. With advanced technology integration, many models offer automation options to enhance efficiency further.
Maintenance is also user-friendly; regular checks on seals and hoses keep the machine running smoothly. Their reliability not only boosts productivity but also contributes to overall operational cost savings in the long term.
Tips for maintaining and
When investing in a durable filling machine for industrial use, it’s crucial to prioritize maintenance. Regular upkeep not only extends the life of your equipment but also ensures consistent performance.
Start with routine inspections. Check for wear and tear on key components like seals, gaskets, and valves. Any signs of damage should be addressed immediately to prevent larger issues down the line.
Cleaning is another essential factor. Build-up from different products can lead to inefficiency or contamination risks. Establish a cleaning schedule that aligns with your production cycles to keep everything running smoothly.
Lubrication is often overlooked yet vital. Use appropriate lubricants on moving parts as recommended by the manufacturer. This helps reduce friction and enhances operational efficiency.
Training staff on proper operation techniques is equally important. Well-trained operators are less likely to make mistakes that could cause damage or downtime.
Maintain open communication with your supplier or manufacturer regarding any potential upgrades or modifications that may enhance longevity and performance over time.
By following these tips, you’ll ensure that your durable filling machine remains a reliable asset in your industrial operations for years to come.