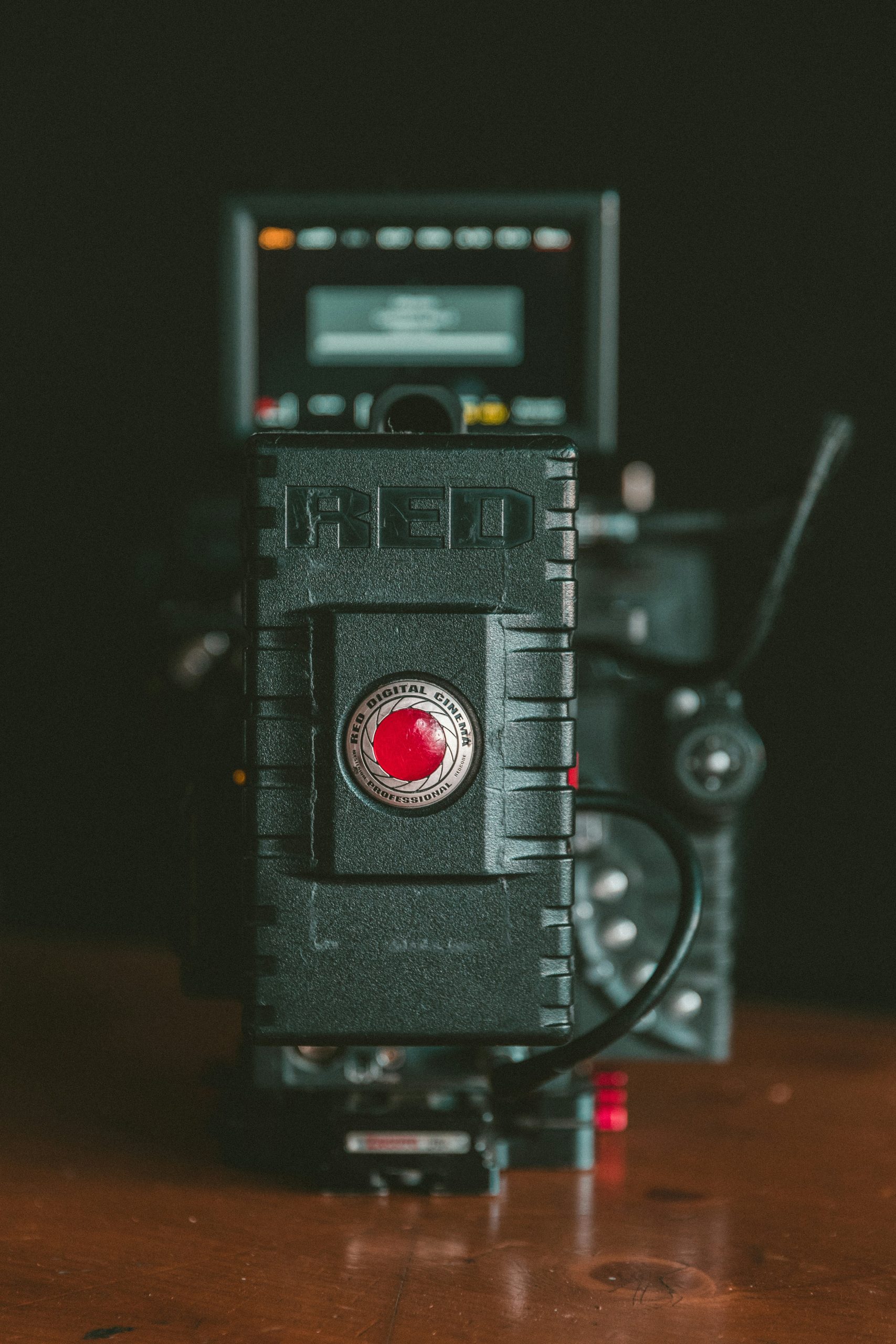
Introduction to Filling Equipment for Startups
Starting a new business is an exhilarating journey filled with countless decisions. For startups in the food, beverage, or cosmetic industries, one crucial choice revolves around filling equipment. This essential machinery can significantly impact efficiency and product quality. However, navigating the landscape of affordable filling equipment for startups can feel overwhelming.
Many entrepreneurs grapple with balancing cost and quality. The right filling equipment doesn’t just streamline operations; it also ensures that your products meet industry standards and customer expectations. As you embark on this adventure, understanding how to choose reliable yet budget-friendly options becomes vital for laying a solid foundation for your business success. Let’s explore what factors to consider when selecting affordable filling equipment without compromising on quality.
Factors to Consider When Choosing Filling Equipment
When selecting filling equipment, startups must first assess their specific needs. The type of product being filled plays a crucial role in this decision. Liquids, powders, and granules each require different machinery.
Next, consider the production volume. High-demand products may necessitate automatic or semi-automatic machines to keep up with output requirements. Conversely, lower-volume operations might benefit from manual options that are easier on the budget.
Speed is another factor to weigh carefully. Your chosen equipment should align with your operational goals without sacrificing quality.
Additionally, think about space constraints within your facility. Compact designs can save valuable room while still delivering efficiency.
Don’t overlook ease of use and maintenance either; user-friendly machines reduce training time and minimize downtime for repairs or adjustments. Always prioritize support from the manufacturer too—it’s essential for long-term success.
Options for Affordable Filling Equipment
When searching for affordable filling equipment, startups have several options that don’t skimp filling equipment on quality. Manual fillers are a popular choice. They require minimal investment and can handle small batches effectively.
Semi-automatic machines offer a middle ground. These systems provide increased speed and efficiency without breaking the bank. They’re perfect for growing businesses looking to scale up production.
Another option is refurbished or used equipment. Many suppliers offer certified pre-owned machinery at reduced prices, ensuring reliability while keeping costs low.
For those in niche markets, tabletop fillers can be ideal. These machines are compact yet versatile enough to meet various filling needs.
Investing in bulk purchase agreements with manufacturers can also lead to discounts on essential filling gear, making it easier for startups to secure the tools they need without overspending.
The Importance of Quality Control in Filling Equipment
Quality control is crucial in the realm of filling equipment. It ensures that every product meets industry standards and customer expectations, which is vital for startups striving to establish a reputation.
Investing in quality control processes helps identify issues early on. This can prevent costly mistakes down the line, saving both time and resources. Moreover, consistent quality boosts consumer trust and loyalty.
Maintaining high standards not only protects your brand but also complies with regulations. Meeting these requirements is essential for avoiding fines or recalls that could derail a budding business.
Regular inspections and calibrations of filling equipment play an important role as well. These practices help maintain accuracy during production, ensuring each unit retains its intended volume and integrity.
In a competitive marketplace, businesses cannot afford to overlook quality control measures. The difference between success and failure often hinges on how well products are crafted from start to finish.
Tips for Maintaining and Repairing Filling Equipment
Regular maintenance is crucial for keeping your filling equipment running smoothly. Schedule routine inspections to catch potential issues early. This proactive approach can save you time and money in the long run.
Cleanliness matters too. Ensure that all parts of the machine are free from debris or residue. A clean workspace not only enhances efficiency but also extends the life of your equipment.
Use quality replacement parts when necessary. While it might be tempting to go for cheaper options, investing in authentic components pays off by reducing downtime and improving performance.
Don’t overlook training for staff operating the machines. Proper handling techniques reduce wear and tear, which prolongs equipment longevity.
Maintain detailed records of repairs and maintenance tasks performed on your filling equipment. This history can help identify patterns over time, guiding future maintenance decisions effectively.
Case Studies: Successful Use of Affordable Filling Equipment by Startups
A local organic juice startup, Fresh Squeeze, faced budget constraints but still needed efficient filling equipment. They opted for a semi-automatic filler that fit within their limited budget. This choice not only streamlined their production process but also maintained the quality of their product.
Another example is Craft Brew Co., which specializes in small-batch beers. They invested in an affordable vacuum filler to manage various bottle sizes without sacrificing taste or presentation. The result was a significant increase in efficiency and customer satisfaction.
These startups showcase how selecting the right affordable filling equipment can lead to impressive growth. By prioritizing functionality and performance over brand names, they found solutions that met both their financial constraints and operational needs. Their success stories inspire others to innovate while staying mindful of costs.
Conclusion: Finding the Right Balance Between Cost and Quality
Navigating the world of affordable filling equipment for startups can be a daunting task. The right choice hinges on understanding both your budget and technology your quality needs. Startups often face pressure to keep costs low while still delivering high-quality products.
Choosing the best equipment means weighing various factors, such as production volume, product viscosity, and required speed. Each startup’s unique circumstances will shape these decisions.
Affordable options abound, but it’s crucial to do thorough research before making a purchase. There are numerous brands that specialize in cost-effective solutions without sacrificing performance or reliability.
Quality control is non-negotiable in any manufacturing process. Ensuring that your filling equipment maintains high standards will save you headaches down the line—both financially and reputationally.
Moreover, proper maintenance plays an essential role in extending the lifespan of your machines. Regular checks can prevent costly breakdowns and ensure smooth operations.
Many startups have successfully implemented affordable filling equipment into their processes and thrived despite initial limitations in funding. Real-world case studies show that smart choices lead to increased efficiency without breaking the bank.
Finding that sweet spot between cost-effectiveness and top-notch quality is not just possible; it’s essential for long-term success in today’s competitive market landscape. Your startup deserves reliable tools that drive growth while fitting within financial constraints.