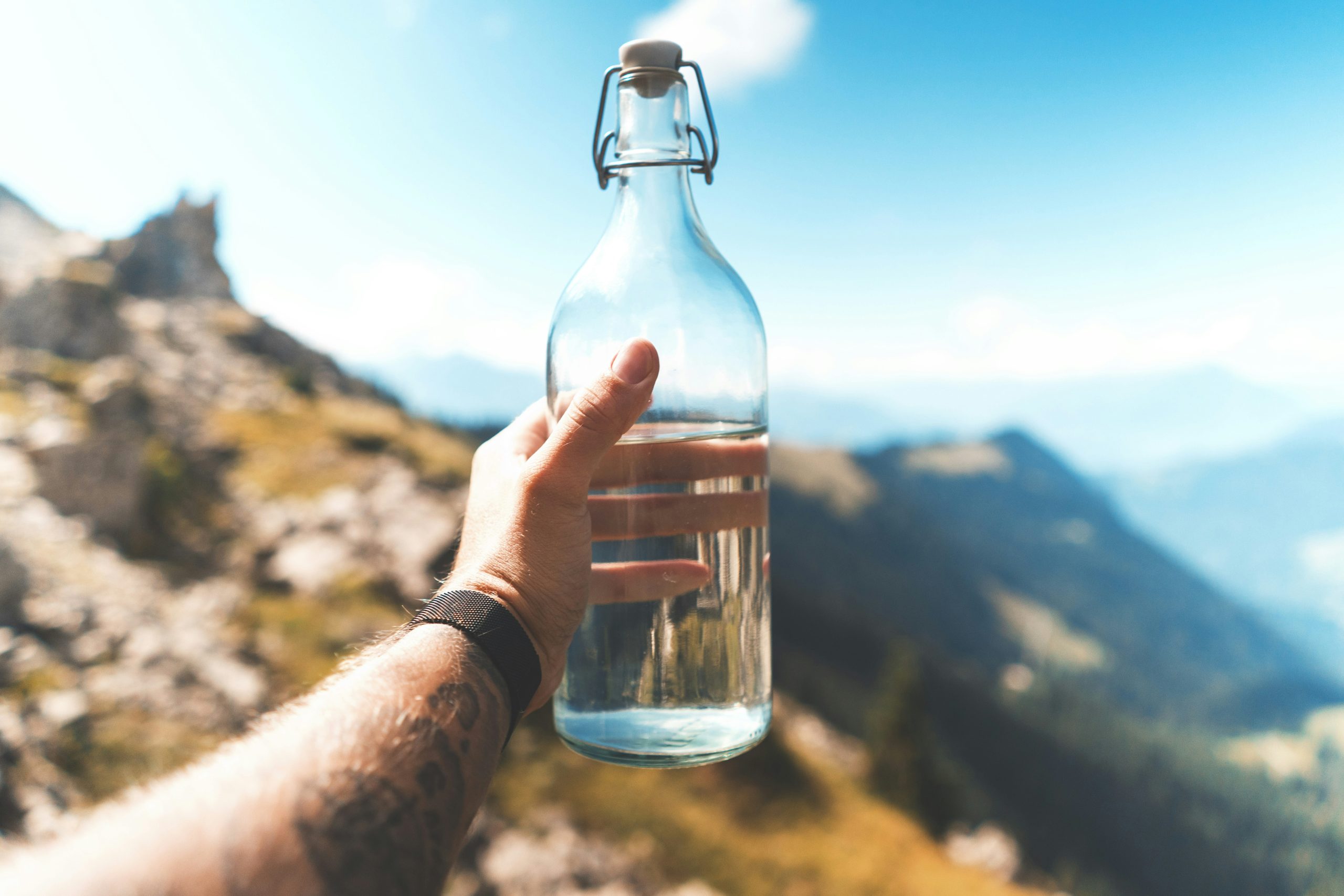
Introduction to Fast Bottle Fillers
The world of production is constantly evolving, and efficiency is the name of the game. When bottle filler it comes to bottling lines, speed and precision can make all the difference. Enter fast bottle fillers—game-changing pieces of equipment designed to elevate high-volume production processes. Whether you’re in beverage manufacturing, pharmaceuticals, or any industry relying on bottles, these machines are revolutionizing how we think about filling.
Imagine a bustling factory floor where every second counts. Workers scurry about while automated systems hum with purpose. In this environment, a fast bottle filler isn’t just a luxury; it’s an essential tool that keeps operations running smoothly and profitably. Let’s dive deeper into why investing in a fast bottle filler for high-volume production could be one of your best business decisions yet!
Benefits of Using a Fast Bottle Filler in Production
A fast bottle filler can significantly enhance production efficiency. With the ability to fill bottles at a rapid pace, manufacturers can meet high demand without sacrificing quality. This speed reduces bottlenecks in the production line, allowing for smoother operations.
Consistency is another major benefit. A reliable fast bottle filler ensures that each bottle receives an accurate amount of product every time. This precision minimizes waste and enhances customer satisfaction by delivering a uniform experience.
Additionally, using advanced technology in these fillers often means less manual labor is required. Automation reduces human error and frees up employees for other critical tasks within the facility.
Faster filling times lead to shorter turnaround periods. Businesses can respond quickly to market changes and maintain their competitive edge in an ever-evolving landscape.
Types of Fast Bottle Fillers Available
When exploring fast bottle fillers, it’s essential to understand the various types available. Each type offers unique features that cater to specific needs.
Gravity fillers utilize gravity to fill bottles quickly and efficiently. They are ideal for thin liquids like water or juice.
Piston fillers work by using a piston mechanism, making them perfect for thicker products such as sauces or creams. Their precision ensures minimal waste during filling.
Pressure-sensitive fillers operate under pressure, allowing for rapid filling of carbonated beverages without losing carbonation. This is crucial in high-volume settings where speed matters most.
Volumetric fillers measure exact liquid volumes with accuracy. This type is widely used across industries due to its reliability and consistent output.
With these options at hand, businesses can choose the right fast bottle filler tailored to their production requirements.
Factors to Consider When Choosing a Fast Bottle Filler
Selecting the right fast bottle filler involves several key factors. Consider the type of product you are filling. Liquid viscosity and carbonation levels can dictate which machine is best suited for your needs.
Next, technology evaluate production speed requirements. Different models offer varying rates of fill per minute. Choosing one that matches or exceeds your production goals ensures efficiency.
Compatibility with container types is also crucial. Ensure the filler accommodates all sizes and shapes you plan to use without compromising on quality.
Maintenance ease should not be overlooked either; machines requiring less downtime will enhance productivity in high-volume settings.
Budget constraints play a significant role in decision-making. It’s essential to find a balance between cost and features to get the most value from your investment while meeting production demands effectively.
Tips for Efficient Use of a Fast Bottle Filler
To maximize the efficiency of your fast bottle filler, start with proper training for your operators. Understanding the machine’s features and functions is crucial. A well-informed team can troubleshoot issues quickly.
Regular maintenance is vital. Schedule routine checks to ensure all parts are functioning smoothly. This helps prevent unexpected downtime during production runs.
Adjusting fill levels accurately can save time and resources. Use consistent measurements to avoid overfilling or underfilling bottles, which could lead to waste and rework.
Implement a cleaning schedule between shifts or product changes. Keeping equipment clean ensures better performance and reduces contamination risks.
Gather data on production speeds and downtimes. Analyzing this information helps identify bottlenecks in your process, allowing you to make adjustments that enhance overall productivity without compromising quality.
Case Study: Successful Implementation of a Fast Bottle Filler in a Production Facility
A beverage company faced significant challenges with its bottling process. Slow filling times were leading to production delays and dissatisfied customers. The solution was clear: a fast bottle filler for high-volume production.
After thorough research, the facility opted for an advanced automatic fast bottle filler. This system dramatically increased their output, reducing fill time per bottle from 10 seconds to just 3 seconds.
The results were impressive. Within weeks, daily production doubled without compromising quality. Employees reported improved morale due to less manual labor and streamlined operations.
Moreover, the new equipment’s precision minimized waste and ensured consistency across batches—an essential factor in maintaining brand integrity.
Customer feedback soared as order fulfillment became quicker and more reliable than ever before. The implementation proved that investing in technology can yield remarkable returns in productivity and satisfaction.
Conclusion and Future Outlook for Fast Bottle Fillers in the Industry
The future of fast bottle fillers in high-volume production looks promising. As manufacturers strive to meet rising consumer demands, the need for efficiency and reliability is paramount. Fast bottle fillers are becoming essential tools that not only enhance productivity but also ensure consistent product quality.
Innovations in technology are paving the way for even faster, more accurate filling solutions. Automation plays a key role here, allowing facilities to streamline processes while reducing labor costs. Moreover, advancements such as smart sensors and data analytics will enable real-time monitoring of operations.
As industries adapt to new trends like sustainability and eco-friendliness, fast bottle fillers are evolving too. Many models now support biodegradable materials and energy-efficient designs, aligning with environmental goals.
Investing in a fast bottle filler can significantly impact operational success. Companies that embrace this technology stand to gain competitive advantages in their markets. The emphasis on speed without compromising quality will continue driving innovations forward.
Looking ahead, we can expect further developments aimed at enhancing user experience and integration capabilities within existing production lines. Industries willing to adapt will find themselves well-prepared for the challenges of tomorrow’s market landscape.