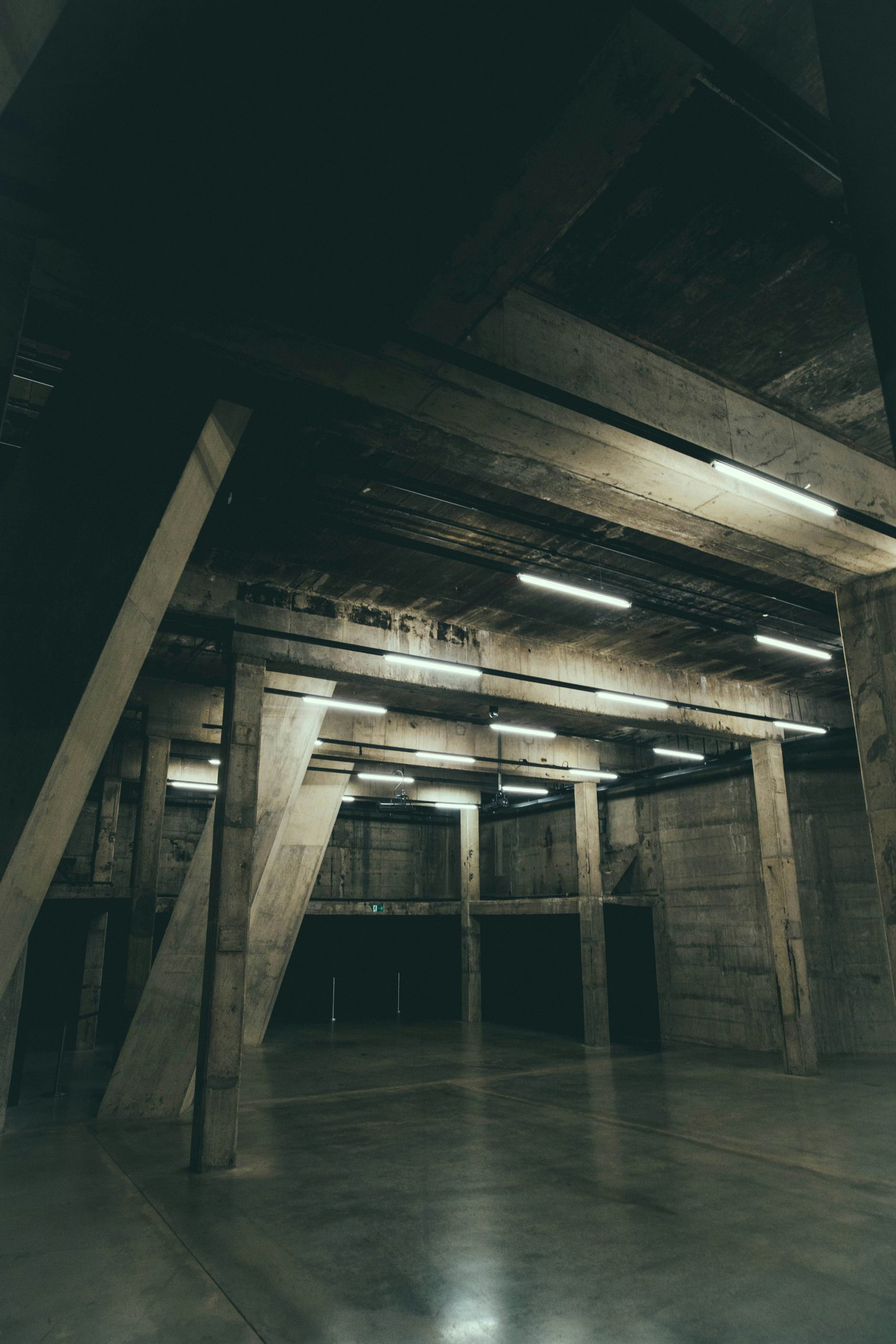
Introduction to High Temperature Sealants
High temperature sealants are the unsung heroes of industrial applications, often overlooked but critical in ensuring operational efficiency. Whether you’re high temperature sealant dealing with high-stress environments or extreme thermal conditions, these specialized sealants play a vital role in maintaining integrity and performance. From manufacturing plants to aerospace engineering, the right high temperature sealant for industrial use can make all the difference.
Imagine machinery running smoothly without leaks or breakdowns caused by heat-induced failures. Picture components that withstand intense temperatures while still delivering peak performance. That’s the power of quality high temperature sealants! In this post, we’ll explore their key features and benefits, various types available on the market, and how they can elevate your operations to new heights. Let’s dive into why investing in these essential materials is not just smart—it’s necessary for success in today’s demanding industrial landscape.
Key Features and Benefits of High Temperature Sealants for Industrial Use
High temperature sealants are engineered to withstand extreme conditions, making them indispensable in industrial settings. One key feature is their ability to endure temperatures exceeding 500°F without losing structural integrity.
These sealants provide excellent adhesion and flexibility, accommodating thermal expansion and contraction within machinery. This not only helps maintain tight seals but also reduces the risk of leaks or failures over time.
Additionally, many high temperature sealants resist chemicals, moisture, and environmental factors. This durability ensures long-lasting performance even in harsh environments.
Another notable benefit is reduced downtime for maintenance. With reliable sealing solutions, industries can operate more efficiently while minimizing costly repairs or replacements caused by seal failure.
Using a high temperature sealant enhances safety measures as well by preventing hazardous leaks from occurring in sensitive areas of operation.
Different Types of High Temperature Sealants and Their Applications
High temperature sealants come in various formulations, each tailored for specific industrial applications. Silicone-based sealants are among the most versatile. They can withstand extreme temperatures while maintaining elasticity, making them ideal for automotive and aerospace uses.
For more demanding environments, ceramic-based sealants offer superior thermal resistance. These are commonly used in furnace linings and exhaust systems, where exposure to intense heat is routine.
Another option is metal-filled sealants, which provide exceptional strength and durability. Often utilized in machinery repairs, they ensure a tight bond that stands up to thermal cycling.
Polyurethane sealants combine flexibility with chemical resistance. They’re suitable for applications involving insulation materials or areas exposed to moisture alongside high temperatures.
Each type of high temperature sealant has unique properties suited for different challenges within industrial settings. Choosing the correct one can significantly enhance performance and longevity.
Factors to Consider When Choosing a High Temperature Sealant
Choosing the right high temperature sealant for industrial use involves several crucial factors. Start by evaluating the temperature range the sealant can withstand. Different applications may require varying levels of heat resistance.
Next, consider the chemical compatibility with fashion substances that will be in contact with your sealant. This ensures longevity and avoids degradation over time.
Also, think about curing time. Some projects may necessitate a quick-drying option to minimize downtime.
Another aspect is flexibility under stress; this characteristic helps maintain an effective seal even when subjected to thermal expansion or contraction.
Pay attention to application methods—some sealants are easier to work with than others, impacting overall efficiency on-site. Taking these considerations into account will lead you toward making informed decisions tailored to your specific needs.
Proper Application Techniques for Maximum Performance
To achieve maximum performance with high temperature sealant for industrial use, proper application techniques are essential. Start by thoroughly cleaning the surfaces to remove any dirt, grease, or old sealant. This ensures a strong bond and optimal adhesion.
Next, apply the sealant evenly. Use a caulking gun for precision and control. Maintain consistent pressure to avoid air bubbles or gaps that could compromise effectiveness.
It’s also crucial to follow the manufacturer’s instructions regarding curing time and ambient conditions. High humidity or low temperatures can affect how well the sealant performs.
Allow adequate time for curing before exposing the sealed area to heat or pressure. Rushing this process may lead to premature failure of the sealants’ properties, negating their benefits in high-temperature environments. A little patience during application goes a long way in ensuring durability and functionality.
Case Studies: Real-Life Examples of Improved Performance with High Temperature Sealants
In a power generation facility, engineers faced recurring leaks in high-temperature pipes. They switched to a premium high temperature sealant for industrial use. The result? A significant reduction in downtime and maintenance costs.
Another example comes from the automotive industry. A manufacturer adopted a specialized high temperature sealant during engine assembly. This enhanced their product reliability while boosting overall performance metrics by 20%.
A major aerospace company also benefitted greatly. By applying an advanced silicone-based high temperature sealant on critical components, they increased operational efficiency and extended the lifespan of parts subjected to extreme conditions.
These case studies highlight how effective sealing solutions can lead to tangible improvements across various sectors, emphasizing the importance of choosing quality materials tailored for specific applications.
Safety Precautions and Handling Guidelines for High Temperature Sealants
When working with high temperature sealants, safety should always be your top priority. Start by wearing appropriate personal protective equipment (PPE), including gloves, goggles, and masks. This protects against skin irritation and inhalation of fumes.
Ensure proper ventilation in the workspace to minimize exposure to harmful vapors. Open windows or use exhaust fans when necessary.
Always read the manufacturer’s instructions carefully before use. Each product may have specific handling guidelines that are crucial for safety.
Store sealants in a cool, dry place away from direct sunlight or heat sources. Keep them tightly sealed to prevent contamination.
Dispose of any unused material according to local regulations to avoid environmental hazards. Always keep these products out of reach of children and pets for added safety.
Following these precautions will help ensure a safe environment while maximizing the effectiveness of high temperature sealants during industrial applications.
Conclusion: The Importance of Using Quality High Temperature
The significance of utilizing high-quality high temperature sealants in industrial applications cannot be overstated. These specialized products not only enhance the durability and longevity of equipment but also significantly improve overall operational efficiency.
Investing in reliable high temperature sealants ensures that machinery operates smoothly even under extreme conditions. This reduces downtime, lowers maintenance costs, and ultimately enhances productivity. Choosing the right product tailored to specific needs can lead to remarkable performance improvements.
Quality matters when it comes to sealing materials exposed to heat and harsh environments. The difference is evident in performance metrics, safety standards, and long-term savings. Prioritizing quality translates into better results for any industrial operation aiming for excellence in their processes.
By understanding the unique features, benefits, types, and application techniques associated with these sealants, businesses can make informed decisions that promote success. Embracing quality solutions today paves the way for a more efficient tomorrow.