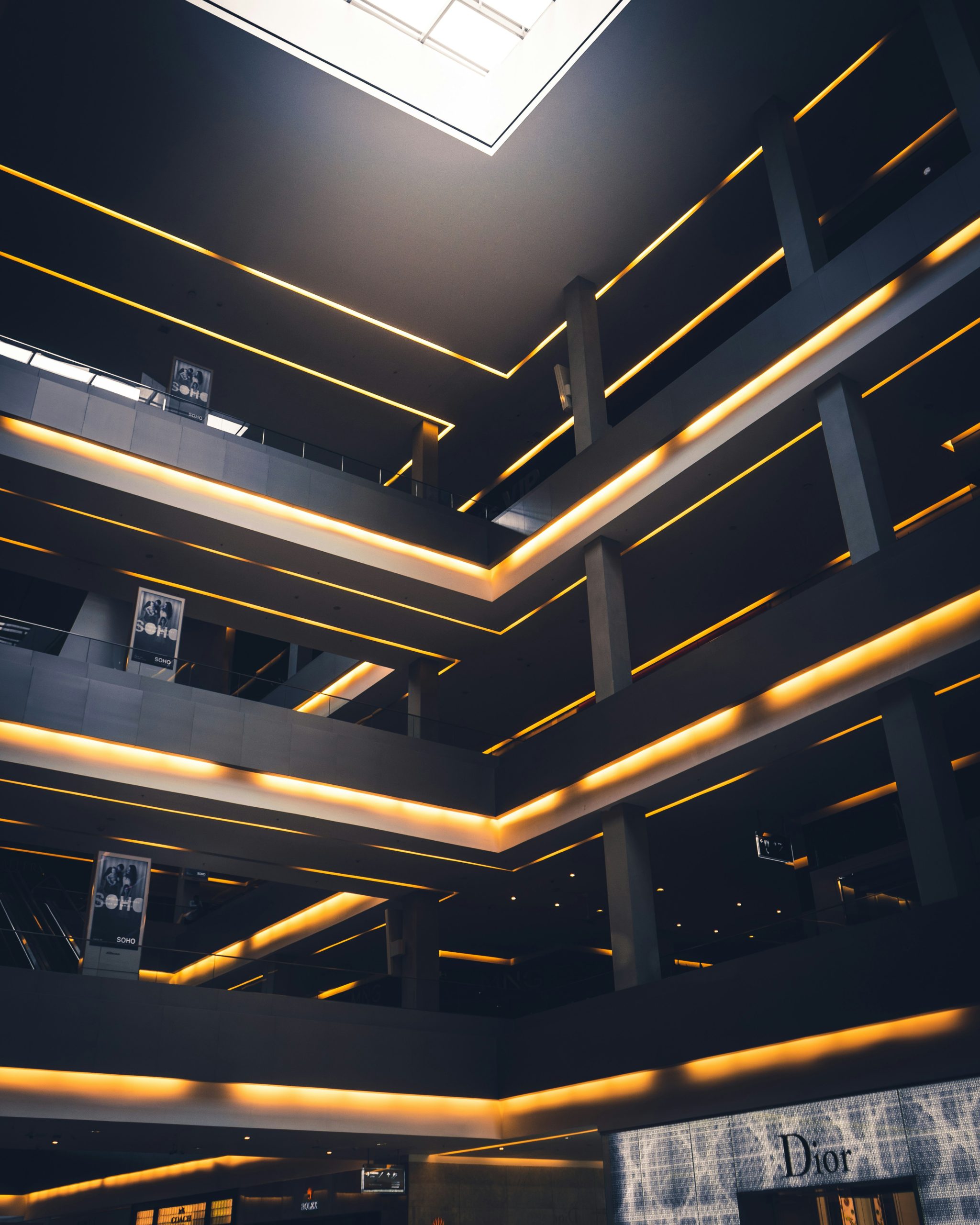
Introduction to advanced packing lines
In the fast-paced world of manufacturing, efficiency is king. As industries evolve, so do their packing strategies. Enter advanced packing lines for large-scale production—a game-changing solution that elevates packaging processes to new heights. These innovative systems not only streamline operations but also bring a host of benefits that can transform how businesses approach packaging.
Imagine a scenario where every product is packed with precision and speed, minimizing waste while maximizing productivity. This isn’t just a dream; it’s the reality made possible by advanced packing lines. From small startups to massive enterprises, these automated solutions are paving the way for smarter production methods that cater to today’s demanding market needs.
Let’s dive into the advantages these cutting-edge systems offer and explore why they’re becoming essential in modern manufacturing environments.
Increased efficiency and productivity
Advanced packing lines for large-scale production transform workflows. They streamline processes, allowing businesses to process larger volumes in less time.
Automation plays a key role here. Machines handle repetitive tasks with speed and precision that human labor cannot match. This reduces bottlenecks, ensuring smooth operations from start to finish.
Moreover, these systems often integrate seamlessly with existing technology. Real-time data analytics monitor performance metrics, enabling quick adjustments when necessary.
This adaptability leads to higher output rates. When every second counts, advanced packing lines keep the product moving efficiently through each stage of packaging.
As a result, companies can meet consumer demand without compromising quality or deadlines. The outcome is an impressive boost in overall productivity that sets them apart in competitive markets.
Cost savings through automation
Automation in advanced packing lines for large-scale production significantly reduces labor costs. By minimizing the need for manual intervention, companies can allocate their human resources more efficiently.
With machines handling repetitive tasks, errors decrease. This not only leads to less waste but also ensures that materials are used optimally. Over time, these savings add up.
Moreover, automated systems often operate faster than human workers. This increased speed means higher output levels within the same timeframe.
Maintenance is another area where automation shines. Modern machinery requires less frequent servicing compared to older models or fully manual setups. This leads to reduced downtime and greater overall efficiency.
Investing in automated packing solutions may seem hefty initially, but the long-term packing lines financial benefits often outweigh this upfront cost dramatically. Companies find themselves reaping rewards year after year as they streamline operations and boost profitability through smart technology integration.
Improved quality control and consistency
Advanced packing lines for large-scale production significantly enhance quality control and consistency. Automated systems minimize human error, ensuring that each product is packed to the same high standard.
Sensors and cameras monitor every phase of the packaging process. This real-time feedback allows immediate adjustments when deviations occur, maintaining tight tolerances on dimensions and weight.
Consistent results boost consumer trust. When customers know they will receive a product meeting specific standards every time, brand loyalty strengthens.
Moreover, data analytics play a crucial role in identifying patterns or recurring issues. By analyzing this information, manufacturers can implement proactive measures to improve processes continuously.
This focus on precision not only enhances customer satisfaction but also reduces waste from defective products. In essence, advanced packing lines create an environment where quality is woven into every step of production.
Enhanced safety measures
Advanced packing lines for large-scale production come equipped with several safety features. These enhance the well-being of workers and minimize accidents.
For instance, many systems include emergency shut-off buttons that allow operators to halt operations instantly in case of an emergency. This rapid response can prevent serious injuries or equipment damage.
Moreover, advanced sensors monitor machine performance continuously. They detect any anomalies and alert staff before issues escalate into dangerous situations.
Ergonomic designs also play a crucial role. By reducing strain on employees during repetitive tasks, these innovations help lower the risk of musculoskeletal disorders.
Regular maintenance schedules integrated into these systems ensure that all components function correctly and safely. This proactive approach fosters a secure working environment while maximizing productivity levels across the board.
Flexibility in packaging options
Advanced packing lines for large-scale production offer remarkable flexibility in packaging options. This adaptability allows manufacturers to respond swiftly to market demands.
Different products require different technology packaging styles. Advanced systems can handle a variety of materials, sizes, and shapes with ease. Whether it’s bottles, boxes, or bulk containers, these lines accommodate diverse needs seamlessly.
Moreover, quick changeovers are possible with modern technology. Businesses can switch from one product line to another without extensive downtime. This agility is vital for staying competitive in fast-paced markets.
Customization is also a significant advantage. Companies can tailor their packaging designs according to branding requirements or consumer preferences. This personalized touch helps stand out on crowded shelves.
Flexibility not only boosts efficiency but also enhances customer satisfaction by meeting specific demands quickly and effectively.
Impact on large-scale production industries
Advanced packing lines significantly reshape large-scale production industries. They streamline operations, allowing companies to meet rising demands without sacrificing quality.
These automated systems minimize human errors and enhance speed. As a result, organizations can produce larger quantities in shorter timeframes.
Moreover, they adapt quickly to market changes. When product specifications shift or new products emerge, advanced packing lines offer the flexibility needed. This adaptability is crucial in today’s fast-paced environment where consumer preferences change rapidly.
Sustainability also benefits from these innovations. Many advanced packing solutions use eco-friendly materials and reduce waste during packaging processes.
As industries embrace these advancements, they witness improved supply chain efficiency too. Enhanced coordination between production and distribution becomes possible, further boosting overall performance in competitive markets.
Potential drawbacks of advanced packing lines
While advanced packing lines offer numerous benefits, they also come with some potential drawbacks. One significant concern is the initial investment cost. Businesses may face high upfront expenses for equipment and technology.
Maintenance can also be a challenge. Advanced systems often require specialized knowledge to operate and repair, which can lead to increased downtime if issues arise. Organizations must ensure that their staff are adequately trained.
Moreover, depending on automation might reduce job opportunities in certain sectors. Employees who perform manual tasks may find themselves displaced as machines take over these roles.
Complexities in system integration could arise when trying to merge new lines with existing processes. This can lead to disruptions during the transition period, affecting overall productivity temporarily. Balancing innovation with operational stability remains a crucial consideration for companies exploring advanced packing solutions.
Conclusion
The landscape of large-scale production is evolving rapidly, and advanced packing lines are at the forefront of this transformation. By enhancing efficiency and productivity, these systems are revolutionizing how businesses operate. The cost savings achieved through automation make it an appealing option for companies looking to maximize their profit margins.
Beyond financial benefits, improved quality control ensures products meet high standards consistently. This not only enhances brand reputation but also fosters customer loyalty. Additionally, with enhanced safety measures in place, employees can work with greater peace of mind.
Flexibility in packaging options allows businesses to adapt quickly to market demands, giving them a competitive edge. Industries such as food and beverage, pharmaceuticals, and consumer goods have all felt the positive impact of these innovations.
While there may be potential drawbacks—like initial costs or training requirements—the advantages often outweigh these concerns significantly. As technology continues to advance, integrating sophisticated packing solutions may just become essential for thriving in a fast-paced marketplace.
With this shift towards efficiency and innovation in packaging processes, it’s clear that companies leveraging advanced packing lines for large-scale production stand poised for success.