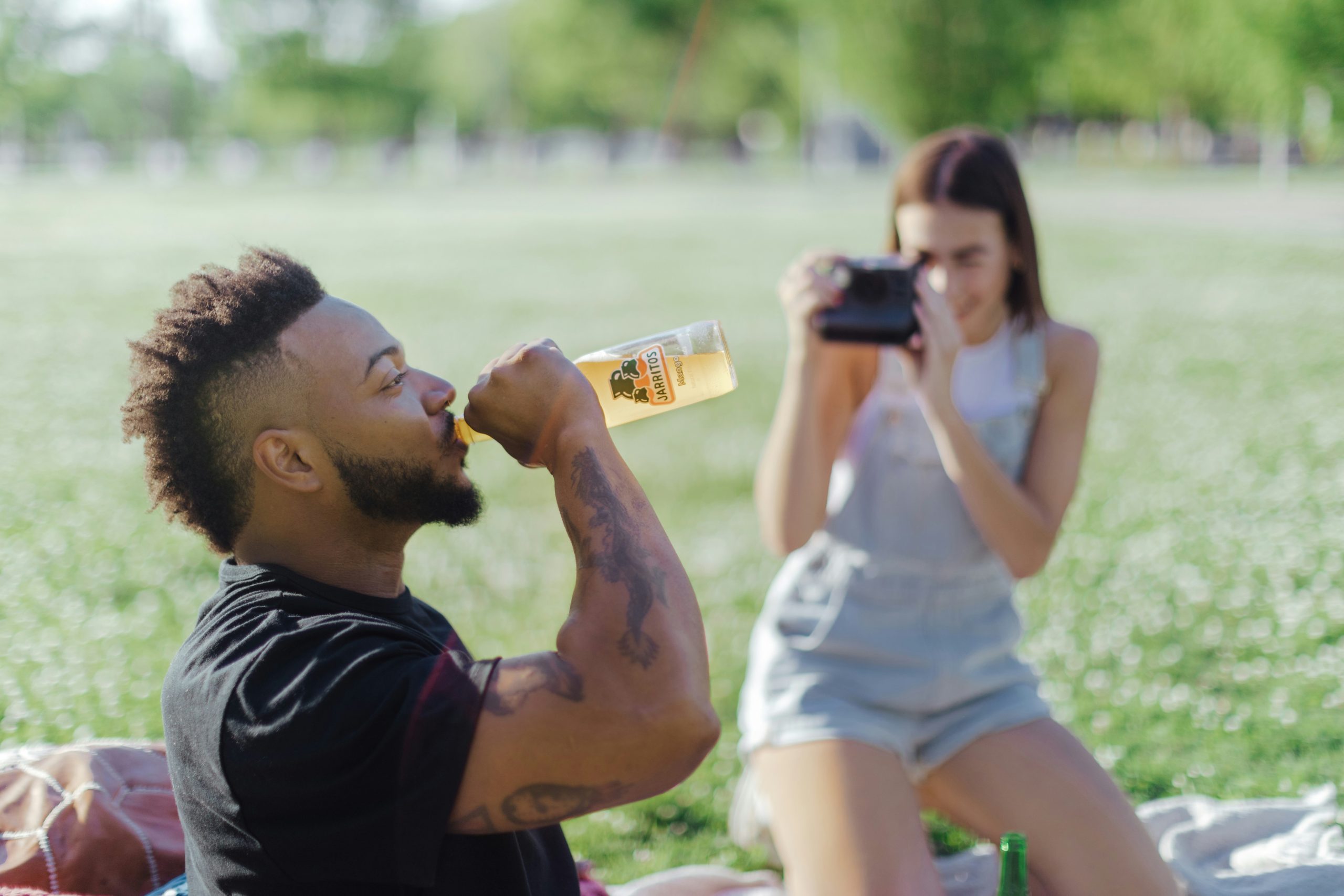
Introduction to the Beverage Production Industry
The beverage production industry is booming, with new players entering the market every day. From craft breweries to artisanal juice makers, the variety of drinks available today is astounding. As consumer demands grow and competition intensifies, producers face mounting pressure to deliver high-quality beverages quickly and efficiently.
This is where an automatic filling line for beverage production comes into play. It’s not just a piece of machinery; it’s a game-changer for businesses aiming to scale up operations while maintaining top-notch quality. Whether you’re a seasoned manufacturer or just starting out in this dynamic industry, understanding the importance of an automatic filling line can make all the difference in your path to success. Let’s dive deeper into why investing in such technology is crucial for any modern beverage producer looking to thrive in this competitive landscape.
What is an Automatic Filling Line?
An automatic filling line for beverage production is a sophisticated system designed to streamline the bottling process. It integrates various machines that work in harmony to fill, cap, and label containers with precision.
These lines can handle different types of beverages, from carbonated drinks to juices and even dairy products. The automation optimizes every stage of production, reducing human intervention while increasing speed.
Key components include filling machines, conveyor systems, capping stations, and labeling equipment. Together they ensure high-volume output without sacrificing quality or consistency.
The technology behind these systems allows for quick adjustments to accommodate varying container sizes and product formulations. This flexibility makes them invaluable for manufacturers looking to adapt quickly in a competitive market.
Benefits of Using an Automatic Filling Line
An automatic filling line for beverage production offers numerous advantages that can transform operations. First and foremost, it significantly boosts efficiency. With automation, the speed of filling bottles or cans increases dramatically compared to manual processes.
Quality control is another major benefit. These systems are designed to ensure consistent fill levels and minimize spillage. This results in a better product for consumers and reduces waste.
Cost savings also play a vital role in decision-making. Although the initial investment may seem high, the long-term savings from reduced labor costs and increased output provide substantial returns on investment.
Furthermore, flexibility is enhanced with an automatic filling line. They can be adjusted to accommodate various container sizes and types of beverages without extensive downtime or reconfiguration efforts.
A. Increased Efficiency
An automatic filling line for beverage production dramatically enhances operational efficiency. By automating the filling process, businesses can significantly reduce manual labor requirements. This allows staff to focus on more critical tasks rather than repetitive actions.
Speed is another key factor. These systems can fill bottles or cans at a pace that humans simply cannot match. This rapid output not only boosts productivity but also meets rising consumer demand effectively.
Consistency in performance is automatic filling line yet another benefit of automation. Unlike manual processes that can vary due to human error, machines deliver uniform results every time. This reliability ensures fewer delays and minimizes waste caused by errors during filling.
Integrating an automatic filling line streamlines workflow across the production floor, optimizing overall operations while keeping up with market trends and customer expectations.
B. Improved Quality Control
Quality control is a vital aspect of beverage production. An automatic filling line enhances this by ensuring each container is filled to the exact specifications. This consistency minimizes human error and maintains product integrity.
Advanced sensors detect fill levels, preventing underfilling or overfilling. As a result, brands can uphold their reputation for quality without compromise.
Moreover, these systems often include monitoring features that track parameters such as temperature and pressure in real-time. Any deviations trigger alerts, allowing swift intervention before issues escalate.
With automated processes in place, manufacturers can adhere to stringent regulatory standards more easily. This leads to fewer recalls and increased consumer trust in the brand’s products.
Incorporating an automatic filling line not only safeguards against defects but also streamlines overall operations. The end result? Higher customer satisfaction and loyalty built on consistent quality assurance across all beverage offerings.
C. Cost Savings
Investing in an automatic filling line for beverage production can lead to significant cost savings. One of the primary advantages is reduced labor costs. Automation minimizes the need for manual intervention, allowing businesses to streamline their workforce.
Additionally, these systems are designed to optimize material usage. They ensure precise filling, which reduces waste and maximizes product yield. This efficiency translates directly into lower raw material expenses over time.
Maintenance costs often decrease as well. Modern automatic filling lines are built with durable materials and technology that require less frequent servicing compared to older equipment.
Moreover, faster production technology cycles mean quicker turnaround times on orders. This agility allows companies to respond rapidly to market demands without incurring additional operational costs. Investing wisely in automation not only boosts productivity but also significantly enhances a company’s bottom line.
Factors to Consider When Choosing an Automatic Filling Line
Selecting the right automatic filling line for beverage production involves several key factors.
First, evaluate your production requirements. Consider how much output you need and whether the system can scale with your business growth.
Next, think about the types of beverages you produce. Different liquids require different filling technologies—be it carbonated drinks or viscous smoothies.
Budget is also crucial. Analyze initial costs versus long-term savings to determine a solid return on investment.
Maintenance and support options are worth investigating too. A reliable service team can minimize downtime and keep operations running smoothly.
Review space constraints in your facility. Ensure that the chosen equipment fits comfortably within existing layouts without disrupting workflow.
A. Production Requirements
When selecting an automatic filling line for beverage production, understanding your production requirements is essential. This involves assessing the volume of beverages you plan to produce daily or weekly.
High-demand periods require efficient systems that can handle increased output without compromising quality. Knowing your target production capacity helps in choosing a filling line with appropriate speed and flexibility.
Consideration should also be given to future growth. Will your business expand? If so, opting for a scalable solution might save money down the road.
Additionally, think about the types of containers you’ll use. Different sizes and shapes may necessitate specific machinery adjustments or configurations within an automatic filling line.
Investing time into these considerations lays a strong foundation for successful operations while minimizing downtime during peak seasons.
B. Types of Beverages Produced
The beverage industry is incredibly diverse. Automatic filling lines cater to a wide range of products, from carbonated drinks to juices and dairy alternatives.
For carbonated beverages, precise carbonation levels are vital. An automatic filling line ensures that each bottle maintains the desired fizziness while minimizing waste.
Juice production requires careful handling due to its perishable nature. With an automatic system, fresh juice can be bottled quickly without compromising quality or taste.
Dairy-based drinks present unique challenges as well. The need for hygiene and temperature control makes these beverages ideal candidates for automation in bottling processes.
Craft beer producers also benefit significantly from automated systems. Consistent fills across numerous batch sizes help maintain brand integrity and customer satisfaction.
Each type of beverage has specific needs that an automatic filling line can adeptly address, leading to improved efficiency and product quality throughout the production cycle.
C. Budget and ROI Analysis
When evaluating an automatic filling line for beverage production, budget and ROI analysis are critical steps. Understanding the initial investment is essential. This includes equipment costs, installation fees, and ongoing maintenance expenses.
Next, consider the potential return on investment. Analyze how much time you can save with automation versus manual processes. Increased speed often translates to higher output and revenue over time.
Don’t forget to factor in labor cost reductions as well. An automated system may require fewer operators or allow existing staff to focus on higher-value tasks.
Conducting a thorough financial analysis will help determine if the benefits outweigh the costs. It’s not just about immediate savings; it’s also about long-term gains that align with your growth strategy in a competitive market environment.
Case Study: Successful Implementation of an Automatic Filling Line
A small craft brewery recently faced challenges with its manual filling process. Slow production rates and inconsistent bottle fills were hindering growth. They decided to invest in an automatic filling line for beverage production.
After the installation, productivity soared by 50%. The new equipment streamlined operations, allowing them to focus on brewing quality beer instead of tedious bottling tasks.
Quality control improved significantly, as the automated system ensured precise fill levels and reduced spillage. This led to fewer customer complaints and higher satisfaction rates.
The brewery also noticed a substantial reduction in labor costs over time. Employees shifted from repetitive tasks to more engaging roles within the company, fostering creativity and innovation.
As demand grew, this investment became crucial for scaling up production without sacrificing quality or efficiency. The success story of this brewery illustrates how strategic choices can transform business outcomes.
Challenges
The journey to implementing an automatic filling line for beverage production is not without its challenges. Transitioning from manual processes or outdated systems can be daunting. Companies may face resistance from staff accustomed to traditional methods, which could lead to a temporary dip in productivity during the adjustment period.
Additionally, selecting the right technology involves navigating a sea of options that vary widely in features and capabilities. It’s crucial to ensure compatibility with existing machinery and workflows, requiring thorough research and planning.
Budget constraints also pose a significant challenge. While investing in an automatic filling line can yield long-term benefits, initial costs may strain financial resources. A careful ROI analysis helps mitigate this risk but demands time and foresight.
Ongoing maintenance and support are vital for success post-implementation. Without proper care, even the best equipment can falter over time. Choosing suppliers who offer robust service agreements becomes essential for continued smooth operations.
Navigating these challenges requires strategic planning and commitment, but overcoming them ultimately leads businesses toward enhanced efficiency and growth within the highly competitive beverage industry.